High-precision subcontract manufacturing
Hygap has a 10 000 m2 production floor full of various types of machine tools working 3-shifts to achieve the highest cost effectiveness and delivery performance. We also have 2700 m2 dehumidified warehouse for raw materials and finished products. Short lead times and a high level of service help us ensure quality throughout every stage – we provide the right parts and the right packaging right on time. If you choose to become a priority customer, we promise 100% delivery precision.
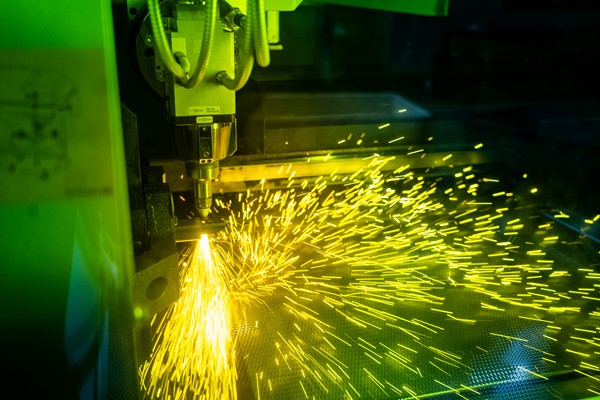
Laser tube cutting
We can offer both 2D and 3D laser tube cutting in stainless steel, mild steel and aluminium based on custom requirements. This provides great flexibility and cost-effectiveness for small dimensions and large, complex components alike.
OUR LASER TUBE CUTTING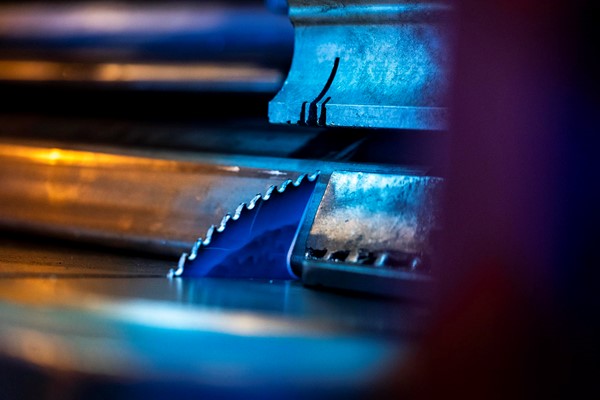
Cutting
We can cut all types of materials in dimensions up to 420 × 420 mm and lengths up to 12 m. Our CNC mitre machine with rod feeder can cut high-precision 60° left and right-hand mitres in large volumes.
Cutting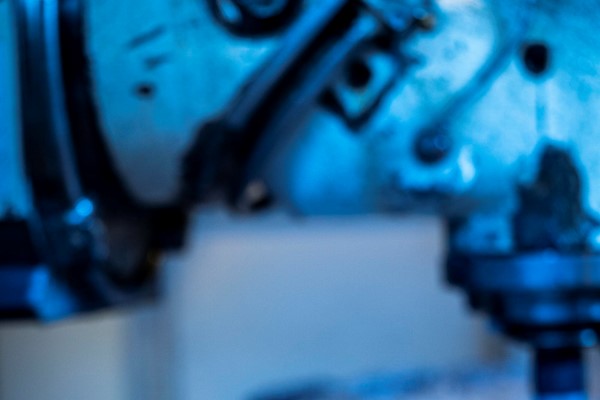
Machining
Our CNC machines are able to turn all types of material up to 350 mm in diameter. Our machining centres and bed milling machines are able to mill all materials up to around 3000 × 1000 mm. We offer great possibilities for machining in automated processes.
Machining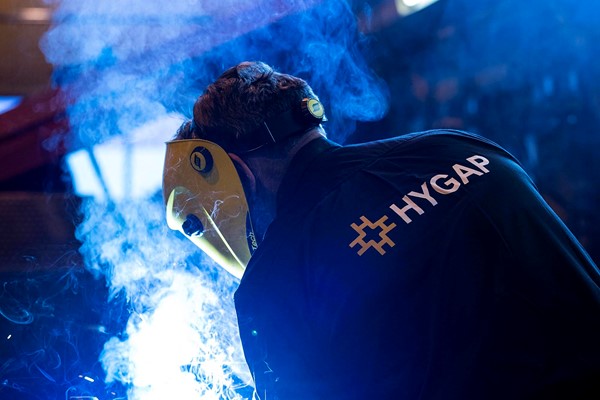
Welding
We weld and join most types of material in both simple and complex structures. We also have the ability to make components as complete and prepared as possible to shorten lead times in downstream production.
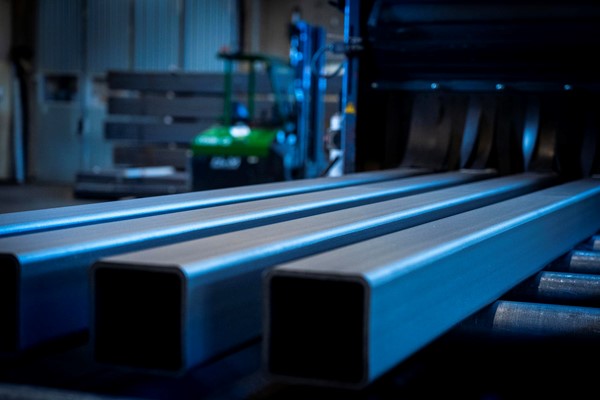
Shot blasting
We use mainly steel balls as blasting media in our 20 metre roller conveyor shot blaster. In it we can blast tubes, profiles, beams and sheet-metal with dimensions up to 1000 × 500 × 6000 mm. Because the machine moves them through the blasting chamber by means of rollers, components are completely blasted upon exit and need not be turned over.
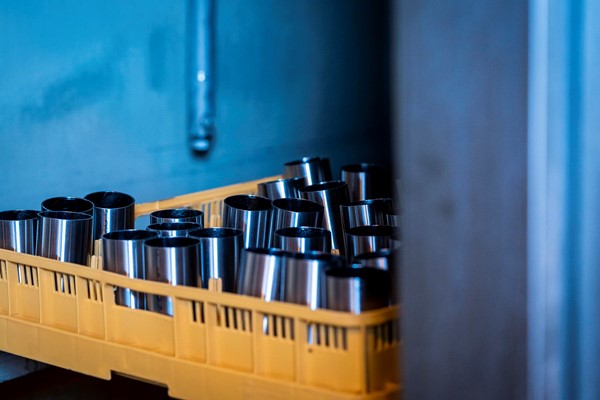
Cleaning
We always seek to deliver clean, high-quality products. Our industrial washing machines can handle profiles and pipes up to 1000 mm. High-volume, small components ranging from 10 to 150 mm are cleaned in our tunnel washer.
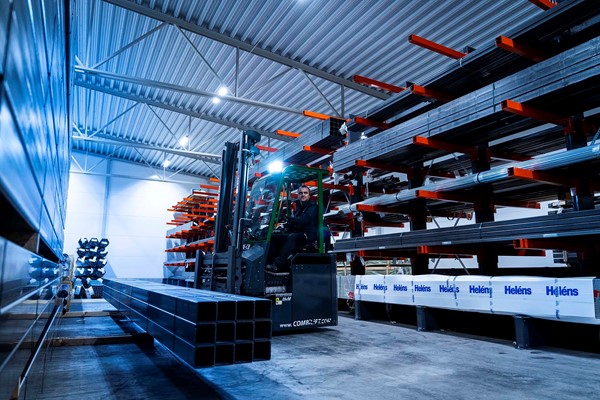
2700 m2 warehouse
We stock tubes and profiles in large quantities in our dehumidified warehouses in order to reduce lead times. Every day, inbound and outbound deliveries totalling 50 to 100 tonnes are handled in well-functioning flows. We also have a department for warehousing a stock of completed products for customers who require the highest delivery precision. Furthermore, we have the ability to package components for delivery straight into production in the most rational manner.
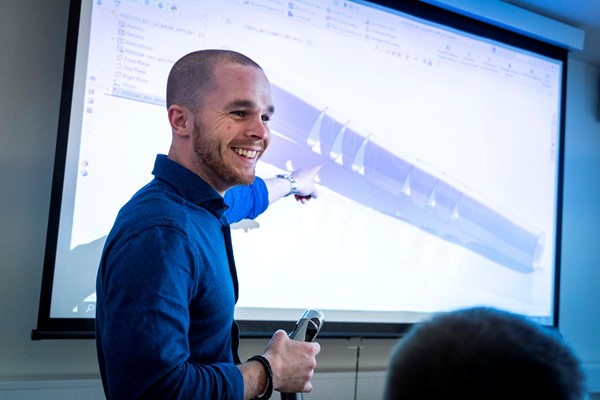
Design
Let us help you to think straight and cost-effectively right from the start. Maybe you have a completed CAD drawing, or perhaps just a simple concept sketch? It’s fine, either way. We go through your idea together to find the best solution. We have engineers on hand when it comes to consultation and design. We work with e.g. Solid Works, Artube and Metrolog.
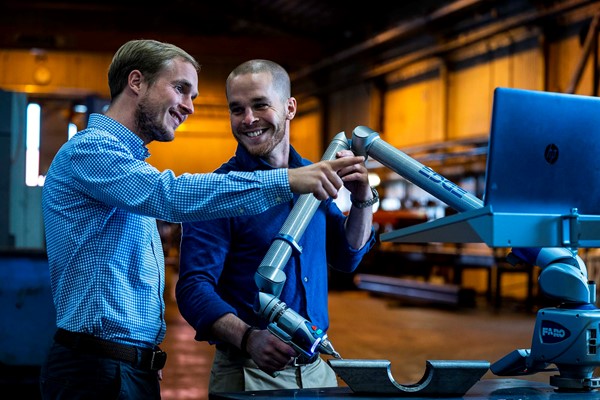
Measuring
Our Faro Edge 7-axis measuring arm can measure completed components to a tolerance of +/-0.04 mm. We can also offer this quality assurance for the measurement of external components
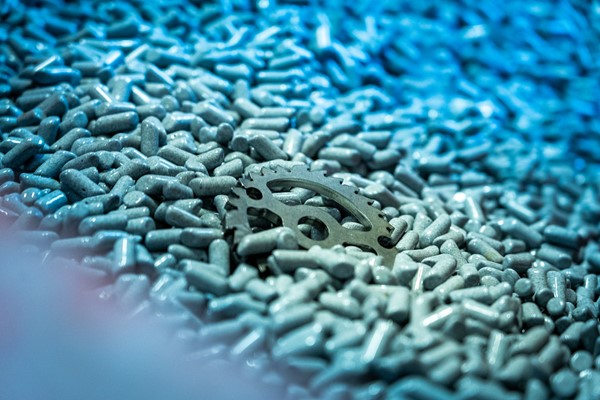
Tumbling
We offer the opportunity for tumbling in our in-house production, where we process the components through grinding and polishing to ensure the removal of burrs and metal residues. By tumbling the components, we achieve the complexity geometetries of the smallest details and maintain the quality imprint on the component.